Strategia frezowania

Frezowanie – rodzaj obróbki skrawaniem, w której ruch obrotowy (główny) zawsze wykonuje narzędzie, a ruchy posuwowe (pomocnicze) mogą być wykonywane zarówno przez narzędzie, jak i przez przedmiot obrabiany (w zależności od konstrukcji obrabiarki nazywanej frezarką). Należy pamiętać, że wpływ na cały proces obróbki mają wszystkie elementy układu OUPN (obrabiarka, przedmiot, uchwyt, narzędzie). Tu zajmiemy się ostatnim czynnikiem, czyli samym narzędziem. W zależności od rodzaju obróbki mamy do wyboru narzędzia składane (z wymiennym ostrzem – płytką wieloostrzową) lub narzędzia monolityczne, które z kolei mogą być wykonane z różnych materiałów (stale HSS, HSSE, stale proszkowe, monolit węglika HM i inne). Jednak niezależnie od rodzaju narzędzia jest kilka kluczowych zasad, o których należy pamiętać podczas generowania ścieżek ruchu narzędzia.
Frezowanie przeciwbieżne i współbieżne.
O frezowaniu przeciwbieżnym mówimy wtedy, kiedy kierunek obrotu narzędzia jest przeciwny do kierunku ruchu posuwowego. W takiej sytuacji grubość wióra rośnie od wartości zero przy wejściu w materiał, aż do wartości maksymalnej przy końcu drogi skrawania. Przy tego typu obróbce występują bardzo duże siły skrawania związane z efektem „wcierania” i wgniatania połączonego z bardzo dużym tarciem i wysoką temperaturą. Pod wpływem tych czynników następuje umocnienie materiału obrabianego, które z kolei wpływa na niższą trwałość narzędzia. Z kolei przy frezowaniu współbieżnym, kiedy kierunek obrotu narzędzia jest zgodny z kierunkiem posuwu, grubość wióra maleje od wartości maksymalnej przy wejściu w materiał obrabiany, aż do wartości zerowej przy jego opuszczaniu. Skutkuje to wydłużeniem trwałości narzędzia, zmniejszeniem sił skrawania i lepszą jakością powierzchni po obróbce. Frezowanie współbieżne jest metodą pierwszego wyboru podczas obróbki.

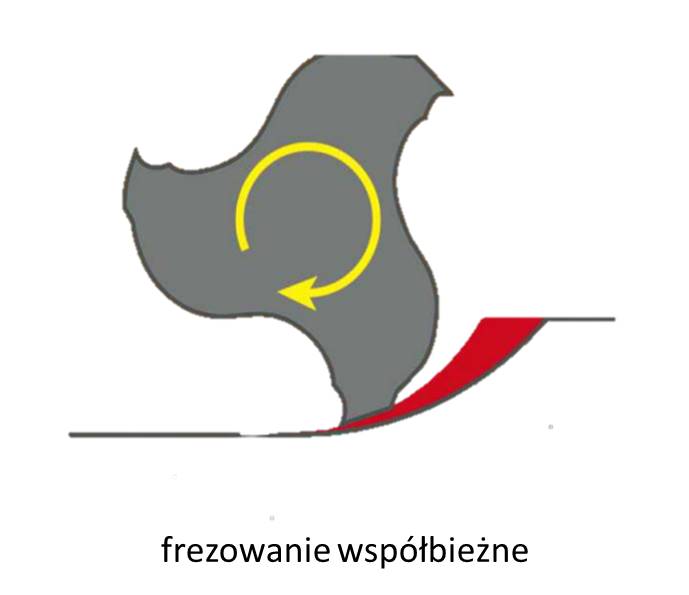
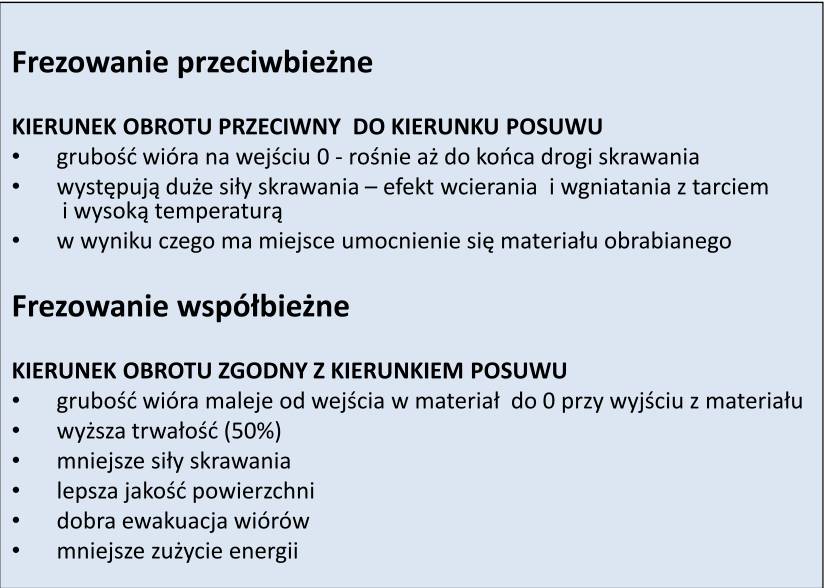
Pozycja narzędzia w stosunku do materiału obrabianego
Szerokość obróbki równa połowie średnicy narzędzia: jest to najczęstszy błąd popełniany podczas generowani ścieżek programu. Przy takim położeniu narzędzia w stosunku do materiału ostrze rozpoczyna skrawanie przy maksymalnej grubości wióra, przez co także wytwarzane są najwyższe siły gnące działające na wrzeciono obrabiarki. Zdecydowanie lepiej, kiedy szerokość warstwy skrawanej jest większa lub mniejsza od połowy średnicy narzędzia. Przy takiej pracy grubość wióra łagodnie zwiększa się do wartości maksymalnej, a następnie maleje do zera (ae>50%D) lub też grubość wióra jest mniejsza od samego początku niż przy pracy połową średnicy narzędzia (wariant ae<50%D). Zarówno jedna, jak i druga pozycja narzędzia generuje znacznie mniejsze siły poprzeczne niż praca połową średnicy.
Wejście w materiał
Zawsze staramy się wprowadzać narzędzie w materiał tak, aby od początku tworzony wiór miał odpowiednią grubość. Przy planowaniu płaszczyzn zdecydowanie lepiej jest wejść w materiał „po łuku” tak, aby na wejściu były generowane grube wióry, a cienkie na wyjściu. Jeśli wprowadzimy narzędzie „po prostej” cienkie wióry będą zarówno na wejściu, jak i na wyjściu, co z kolei wygeneruje wyższe siły skrawania niż przy wejściu „po łuku”.
Kontakt z materiałem obrabianym
Moment wejścia w materiał jest dla narzędzia bardzo trudny. Starajmy się, aby podczas pracy narzędzie miało z materiałem ciągły kontakt. Frezując płaszczyznę nie wykonujmy ruchów „w powietrzu”. Generujmy ścieżki tak, aby unikać tego typu przejść. Dodatkowo – podczas zmiany kierunku pracy narzędzia starajmy się unikać sytuacji w której odbywa się to w sposób gwałtowny. Mówimy tu o tak zwanych „ostrych narożach”. W takiej sytuacji starajmy się, aby zmiana kierunku pracy narzędzia odbywała się po łuku. Dzięki temu zabiegowi narzędzie będzie w sposób stały obciążone wiórem bez zmiany jego objętości. Wpłynie to w bardzo pozytywny sposób na trwałość narzędzia, ale także na jakość powierzchni po obróbce.
Kształt i geometria narzędzia monolitycznego
W zależności od rodzaju wykonywanej obróbki mamy do dyspozycji narzędzia o różnych kształtach. Będą to frezy walcowo – czołowe umożliwiające obróbkę boczną, ale także czołową. Wśród narzędzi PROCUTTER będą to wszystkie frezy o oznaczeniu THM9… Przy obróbce skomplikowanych powierzchni metodą wierszowania będziemy korzystali z frezów promieniowych, których oznaczenie zaczyna się od THM7… Frezy toroidalne (z zaokrąglonymi narożami) możemy wykorzystać przy obróbkach bocznych, czołowych, ale także przy obróbce wykończeniowej powierzchni wypukłych. Ich oznaczenie kodowe to THM5…
Materiał obrabiany
Wśród frezów serii PROCUTTER znajdziemy narzędzia zaprojektowane do obróbki określonych materiałów. Będą się one różniły od siebie zarówno geometrią ostrzy, materiałem bazowym, a także powłoką, która jest dedykowana pod określone materiały obrabiane. Aby ułatwić dobór narzędzia pod określony materiał w naszym katalogu umieściliśmy TABELĘ DOBORU NARZĘDZI która w sposób intuicyjny kieruje nas do określonych kodów tak, aby narzędzie zostało dobrane w sposób optymalny. Zawsze jednak starajmy się korzystać z narzędzi o jak najmniejszej długości. Optymalny wysięg budujmy w oparciu o oprawki, które dostępne są najczęściej w kilku długościach w zależności od konkretnej aplikacji Zachęcamy do zapoznania się z katalogiem narzędzi naszej produkcji: linia PROCUTTER